The Three T’s of Dropped Objects Prevention – Toolbox Talks
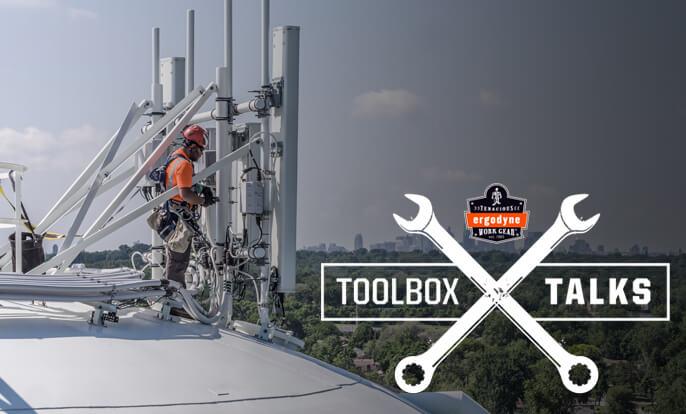
Toolbox Talks are intended to facilitate worksite health and safety conversations. Click here to download talking points on the basics of how to prevent dropped objects by implementing Trapping, Tethering, and Topping on your jobsite.
While preventing people from falling at heights has (thankfully) become standard practice, drops prevention for the tools and equipment they take to heights has been a relatively recent movement.
Typically, the potential dangers of falling objects at job sites are addressed with passive engineering controls like toe boards, netting, barricades and the like. But active controls like those called out in the dropped objects standard are much less common.
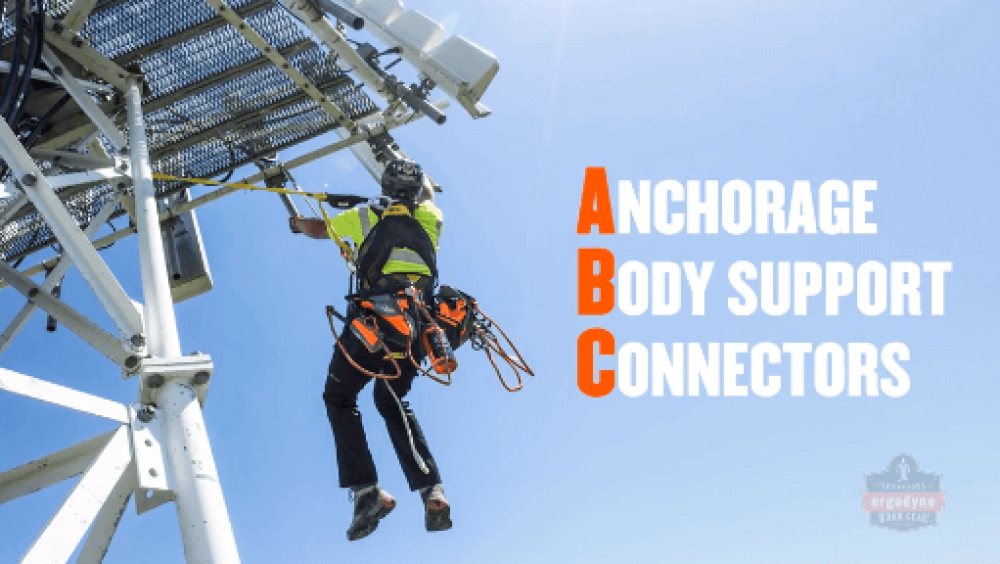
For those working at heights, remembering the types of equipment needed to protect workers is as easy as ABC (Anchorage, Body Wear and Connecting Device).
In dropped object prevention, the “3T’s” are used to categorize the active engineering controls one can easily implement to prevent falling objects on the job. So let’s take a closer look.
Introducing the 3T’s: Trapping, Tethering, Topping...
Trapping
Trapping is a term used to describe the installation of retrofit attachment points on tools and primary anchoring locations -- because the majority of tools don’t come with them built in. These retrofit attachments can adaptively be applied or “trapped” onto these tools and equipment prior to use.
Anchor attachments should be installed onto locations that are secure and are never intended for heavier tools if applied to the individual. Tool attachments come in a variety of designs based on the tools they are intended for and are available in in one or two step applications.
Important: Tool traps should never compromise the integrity of the tool or impede the tool’s primary function.
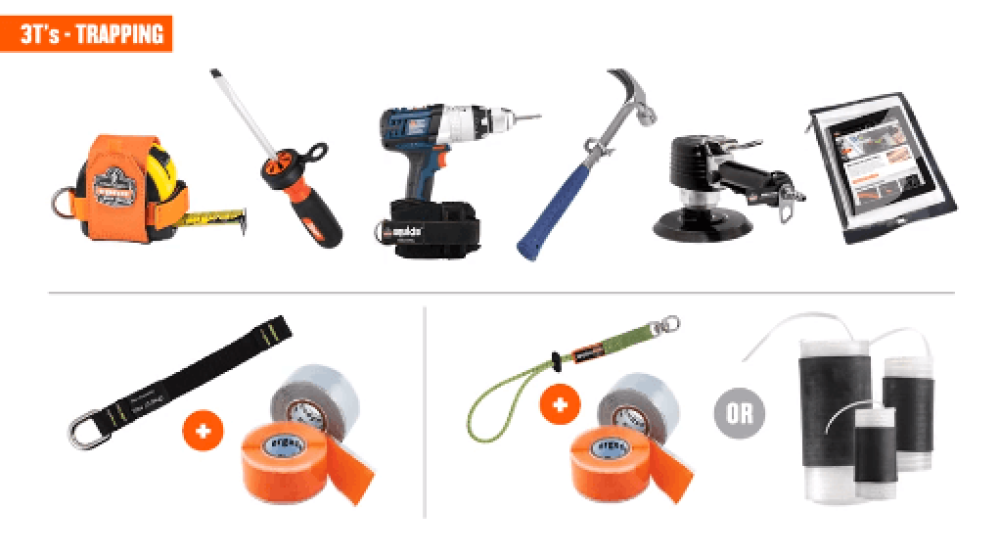
One-Step Tool Attachments
Straightforward “traps” that install with a focused application and are typically intended for more specific tools like: Slips that slide onto screw drivers and hex keys; brackets and wraps that fit specific power tools or tape measures; and sleeves that house cell phones are some examples.
Two-Step Attachments
Involve two separate solutions combined into one attachment. “Tool Tails” are applied onto a tool and then “trapped” by a tape or shrink to secure them.
Tethering
Tethering is the retention of the tools and equipment being used to the anchor points that hold them. This is often achieved through the use of a tool lanyard. These lanyards should have the proper connections on each end for the tools and anchors being used. They should also be made with a shock absorbing design whenever possible.
As tool tethering has evolved, a variety of tool lanyard styles have surfaced.
But most fall into five basic categories:

Wrist Lanyards: Using the wrist as an anchor point, these lanyards slide on easy to minimize drop distances (when clearance is low) and snag hazards that can cause issues.
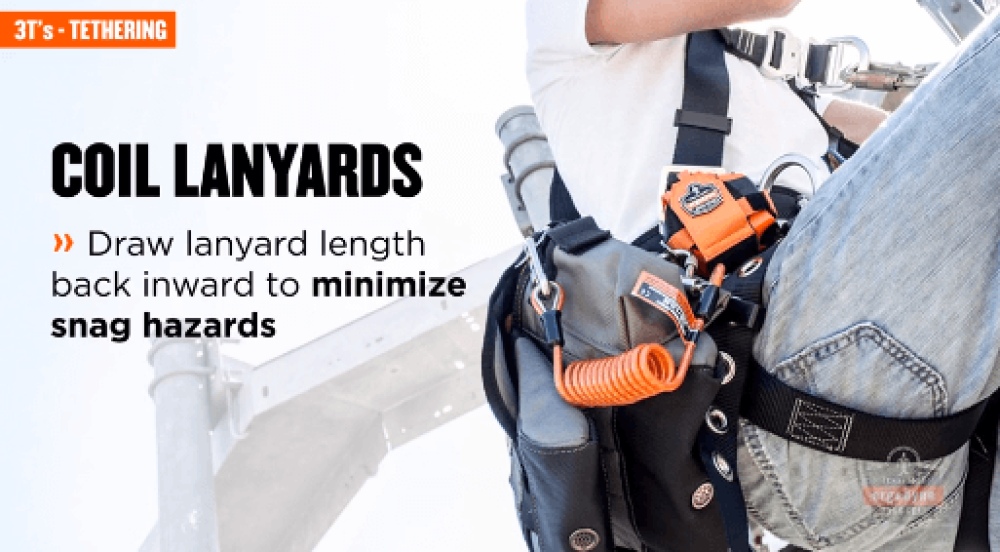
Coil Lanyards and Retractable Lanyards: Designed to avoid snags and hang-ups, Coil and Retractable designs draw the length of the lanyard back inward to keep things neat, tidy and close to the hip.
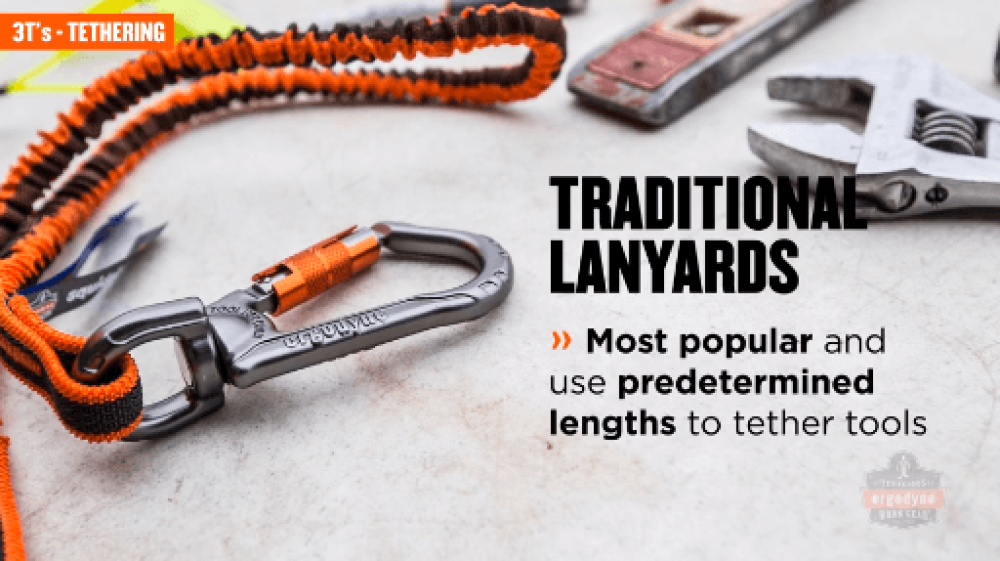
Traditional Lanyards: The most popular option, traditional lanyards use a predetermined length to tether tools. Look for shock absorbing models that reduce the dynamic force on the body or other anchor point if drop occurs.

Specialty Lanyards: From hard hats, mobile devices and more, these lanyards concentrate on specific equipment to tether.
Topping
The 3rd T, “Topping”, consists of the containers workers use to bring tools and equipment to and from heights.
There are two types of containers used:

Tool pouches and bags are typically carried on individuals to keep their contents at hand while working. These often remain stationary.
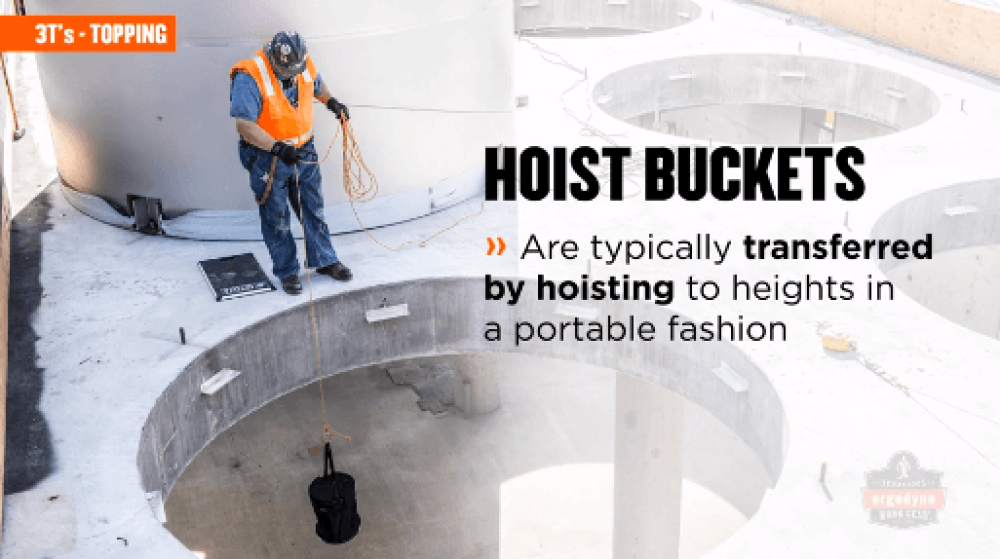
Hoist buckets and bags are transferred by a different means, typically lifting them in a portable fashion to and from heights.
These containers, regardless of type or mode of transportation, should have a secure closure or “top” that can cover contents and prevent them from spilling if tipped.
All containers may have tethering points available to attach tool lanyards, but if a container does not have a secure closure it must have these tethering points available.
TESTING, TAGGING AND SAFETY FACTORS
Safety factors are built into all quality safety equipment. This is especially important when considering the high potential for misuse — folks loading up buckets and bags past their stated capacity, for instance. Ergodyne’s tool lanyards are drop tested with a 2:1 safety factor [e.g. a 10lb (4.5kg) tool lanyard is tested to 20lbs (9.0kg]. Containers are statically tested to a 5:1 safety factor [e.g. 150lb (68kg) bucket is tested to 750lbs (340kg)].